Model Design Drawing
- Model Design Construction
- Model Design Drawing Model
- 3d Model Design
- Artists Models For Drawing
- Model Design Drawing Easy
Looking for downloadable 3D printing models, designs, and CAD files? Join the GrabCAD Community to get access to 2.5 million free CAD files from the largest collection of professional designers, engineers, manufacturers, and students on the planet. With 2D or 3D CAD programs, we can quickly take your sketch and turn it into usable 3D Models and accurate drawings. Rapid 3D can create a 3D model of a design, apply material and light effects, create realistic renders, and document the design with dimensions and other annotations.
Introduction: Presentation: Final Model, Drawings + Renderings
If you have been taking this class with the intention of designing something for your own personal use, then now is the time that you would take your final design and make a finished version in the final material!
We have some great fabrication classes to help you with that if you don't have experience in the material you'd like to use, or just want to brush up on your skills:
Metalworking with randofo
Mold Making & Casting with me
Welding with audreyobscura
Woodworking with mikeasaurus
Lamp Making with me
And classes that cover almost everything electronic.
Depending on the fabrication method you plan to use, this could mean having to make 2D CAD drawings for cutting parts on a CNC machine or creating a 3D rendering for use with a 3D printer. I cover both of these processes below.
If you don't require any further info to move ahead with your final product, then thank you so much for taking my class! And please send me photos of your finished thang.
If you will be presenting your design or handing it off to be manufactured, you will want to follow along with this final lesson.
There are 3 main components to a completed design:
- Presentation model/prototype
- Technical drawings
- 3D rendering
Step 1: A Presentation Model/Prototype
As I mentioned earlier, you can absolutely make most final prototypes using hand and standard studio/workshop tools. The final presentation model is meant to be a clear representation of what the finished product would look like. It doesn't have to function as the finished, manufactured product would, nor does it even have to be out of the same material that the product will be produced in (painted foam is commonly used). It just needs to communicate the form, scale, and look of the product so that others can understand your vision (think movie prop).
Full disclosure: In most cases, a 3D rendering of the finished design will suffice, especially for manufacturing (the image for this lesson is a 3D model of my project NOT a real one!). But if you are trying to get funding or convince someone of the genius that is your new idea, having a physical model that they can see in space and touch is incredibly helpful.
Step 2: Technical Drawings
The job of technical drawings is to visually communicate dimensions, specifications, and how something is constructed. A set of technical drawings is called working drawings, and these are sent to manufacturers so they have all the information they need to work from (shapes, dimensions, material specifications, etc.) when producing your product.
These can still be hand drawn, but if you use a CAD (computer aided design) or vector based software to create your drawings (like AutoCad or Adobe Illustrator), those drawings can also act as a 'pattern' and be exported as a file type that communicates with laser cutters, water jet cutters, etc. – any CNC machine that cuts flat parts. Providing CAD files can save you money, as it will save the manufacturer's from having to generate those drawings themselves.
If you'd like to learn how to make your own rapid prototyped parts form CAD drawings, check out the following free Instructables classes:
Laser Cutting with JON-A-TRON
CNC with JON-A-TRON
A technical drawing usually contains top down drawings of the individual pieces, front, side, and section views –all with dimensions, a 3/4 view of the complete product, and sometimes an exploded view of how the parts fit together.
As I mentioned in the ideation lesson, JON-A-TRON also has a class on Design Sketching that covers all of the terms and how to draw the different views you'll need for your drawings.
If you don't already know how to use a 2D CAD or vector based software, I recommend downloading a free trial version of AutoCad LT and going through their great tutorials.
Step 3: 3D Rendering / Drawing
Generating a 3D model of your product is a great way to:
- create a visual representation of your 'finished' product for use in presentations, pitch decks, and to send to manufacturers to aid production
- get away with NOT having to do your technical drawings in a separate 2D software
3D CAD/CAM (computer aided manufacturing) software will not only create beautiful renderings, but allow you to generate technical drawings with dimensions, do 3D exploded drawings of all the parts – showing how they go together – and export files for 3D printing or CNC machining.
If you're interested in learning how to 3D render and print, I highly recommend trying the 3D CAD/CAM software Fusion 360. Full disclosure, it's an Autodesk product (Autodesk owns Instructables), but it really is just a super easy-to-use, intuitive software. Plus it's FREE for students, teachers, hobbyists, and start-ups!
Autodesk Fusion 360 (free)
This is a powerful 3D modeling platform that's easy to learn but has endless potential. With it, you can design complex 3D objects for practically any kind of fabrication, digital or otherwise.
Click here to sign up for free as a Hobbyist / Enthusiast / Startup or as a Student or Educator.
- Follow one of the links above to download the app (don't use the App Store on Mac).
- Enter your email and download the free trial.
- Install and setup a free Autodesk ID account.
- When you open Fusion, select the Trial Counter in the upper toolbar (it tells you how many days are left on your trial).
- In the next dialog box, select 'Register for Free Use'.
- Sign up as a Start-Up or Enthusiast (Free). You can also Sign up as a Student or Educator (Free) if you're a student or educator at a registered institution. This will give you free use of Fusion 360 for as long as you need it (not just a 30-day trial).
- Select the 'I accept Terms and Conditions' checkbox and click Submit.
Once you've downloaded the software, check out JON-A-TRON's 3D Printing Class. It will take you through creating a 3D rendering step-by-step! And then once you've got a handle on generating those, he'll show you how to 3D print your creation!
NOTE: My 3D renderings were done by Michael Sagan, the head of the Fusion 360 Customer Success Team (I've just started learning the program!) and they also have lots of helpful resources, also know as Virtual Labs that troubleshoot the Fusion 360 learning curve. They also have great webinars you can sign up for coming up on different Fusion 360 features. Check them out!
Another way to get a 3D rendering of your design into a 3D software without having to draw it, is to 3D scan your final prototype. My co-worker MikaelaHolmes has a great (free!) class on 3D scanning using photogrammetry – which means that you don't need an expensive 3D scanner, just a camera! This is an easy and low-tech way to get high tech results!
The future is now. :)
Step 4: Become a Professional Designer
I wrote this class primarily for hobbyist makers and entrepreneurial inventors. Becoming a professional product designer (for a company) would require a much more rigorous education than I'm providing here (i.e.: a degree). :)
If you're interested in pursuing a career in product design, here's a link to a list of some of the top programs in the USA and abroad that was compiled, and well researched, by a prospective student:
What to look for in a program
A good product design program will offer classes in:
- Design drawing/sketching
- Concept development
- Design research
- Design history
- Model making: analog & digital
- Digital visualization: Adobe Photoshop & Illustrator, CAD/CAM software
- Rapid prototyping
- Advanced manufacturing
- Material innovation
- Product life-cycle analysis (sustainable and circular design)
- Services design (human-centered design)
- Design ethics
- Business 101
With a focus on leadership, cross-disciplinary projects, and critical thinking.

Karen Hofmann, chair of product design at Art Center College of Design, says:
'As we move forward, we are anticipating that in the next decade designers will continue to be innovatorsand inventors—but that they will also have the opportunity to take on moresignificant leadership roles in organizations, from startups to leadingmultinational corporations and even governments.'
'As business organizations continue to embrace design, the role of the designer expands as well. Designersare not only responsible for visualizing and making, they now are'facilitators' as the design process has become more participatoryand collaborative inside of organizations as well as with the emergence of openinnovation models.'
There are exciting opportunities for future product designers and for how the design process can be applied.
How to get ahead before you even start
READ / The following books are essential reads for any designer:
The Design of Everyday Things by Don Norman
Emotional Design: Why We Love (or Hate) Everyday Things by Don Norman
The Green Imperative: Ecology and Ethics in Design and Architecture by Victor Papanek
Elements of Design: Rowena Reed Kostellow and the structure of visual relationships by Gail Greet Hannah
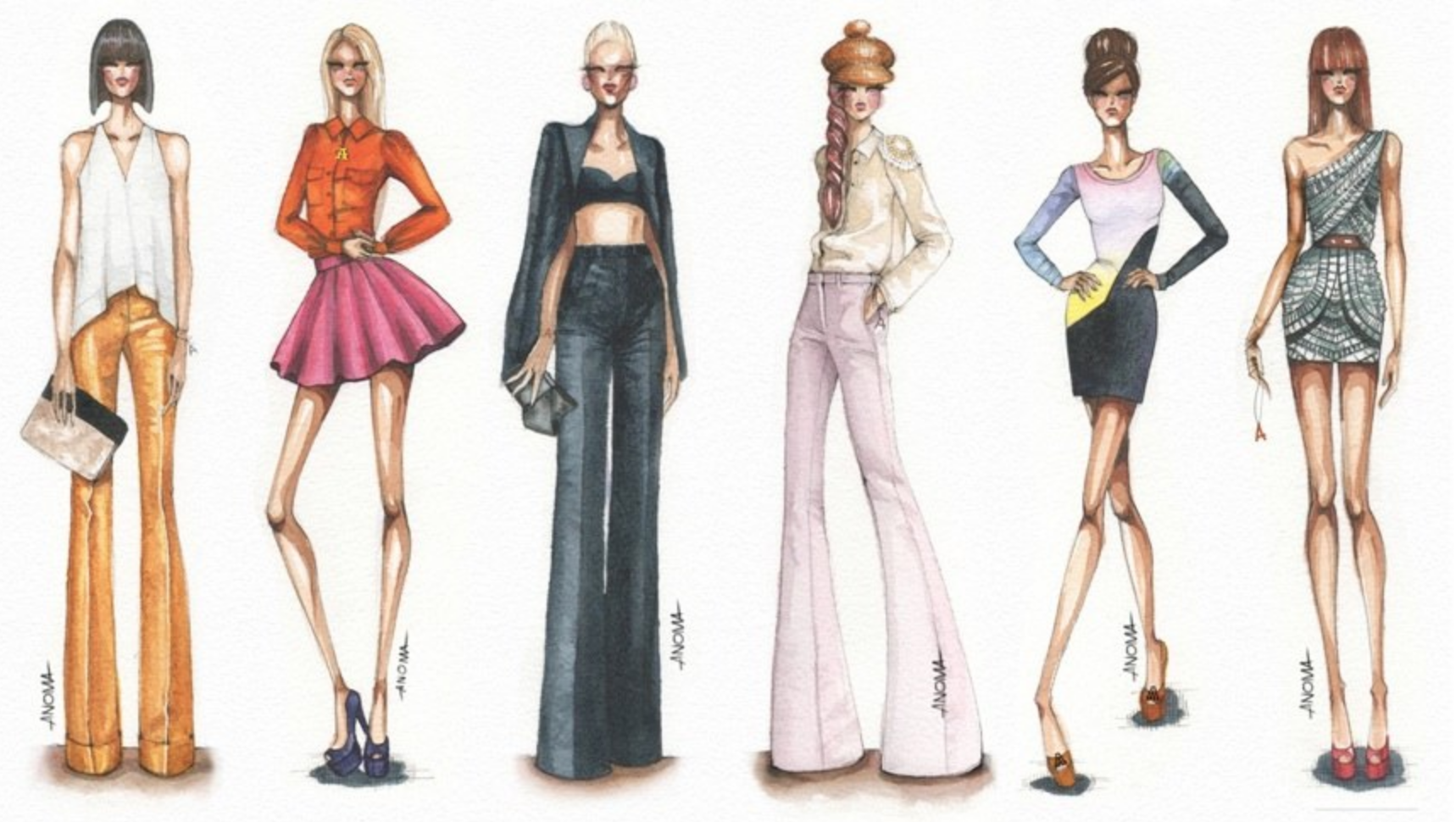
The Laws of Simplicity by John Maeda
Manufacturing Processes for Design Professionals by Rob Thompson
WATCH / Netflix is doing an AMAZING series on different design disciplines called Abstract: The Art of Design (you may need to be logged in to access the link). Every episode is a peek behind the curtain and I found each designer featured incredibly inspiring. WATCH IT!!!!! Do it. Now. Really.
LISTEN / Podcasts are a great source of design thinking, design history, human-ness, and inspiration. My favorites are:
99% Invisible with Roman Mars
Adventures in Design with Mark Brickey
Design Matters with Debbie Millman
OBSERVE & BE INSPIRED / Every day, try to notice details that you maybe have never paid attention to before. How do the things you use work? How do they feel in your hands? How do they look? Which door handles are successful, which are completely counter intuitive. And be inspired by these details!
Step 5: Happy Design Trails!
Thank you for taking my class. :)
Best,
Paige
Be the First to Share
Recommendations
Make it Glow Contest
First Time Author Contest
PCB Challenge
Computer Aided Design
Model Design Construction
CAD is the most effective way to design your product. Using CAD you can simulate, analyze, and create drawings, renderings, 2D drafts, and 3D prints.
Model Design Drawing Model
Drawings & Drafting
Professional, accurate drawings made to your specifications. Rapid 3D can provide the drafts needed for production or patent applications.
Patent Drawings
Submitting a Patent? Rapid 3D can supply any drawings needed, including notes and detailed views.
3d Model Design
Realistic Renderings
Artists Models For Drawing
Life-like 3D renderings can be supplied for websites, advertising, focus groups, or submitting to investors.
Model Design Drawing Easy
Accurate Floor Plans
From 2D overhead views to 3D renderings, we can accurately create your home design, shop layout, or lot layout in CAD. Make sure it works first!
3D Printing
We offer FDM 3D Printing Services in common material such as PLA, ABS, & PET. Test your idea quickly using high quality 3D prints.